Pick-by-Light
Challenges when picking individual parts
Susceptibility to errors when picking
Manually picking many individual parts is a task that is prone to errors. Employees must either know each storage location by heart or look them up frequently, which makes everyday work stressful and time-consuming.
Issues with similar looking parts
It is particularly challenging when it comes to parts that look similar but are required in different combinations and quantities. A manual picking system often reaches its limits here and requires revision.
From your vision
to the real solution
Efficient order picking through “pick-by-light”
Commissioning challenges
The ordering of numerous individual parts, particularly with components that look similar and are required in various combinations, is prone to errors. Employees are faced with the challenge of either knowing each storage location by heart or having to constantly look them up, which leads to stress and inefficient work processes.
“Pick-by-light” as a solution
The introduction of a “pick-by-light” line represents a revolutionary solution, particularly for repetitive individual parts. Each part number is assigned to a fixed storage compartment, which is ideally refilled using a Kanban system. For each picking order, the control system lights up a lamp above the corresponding storage compartment to indicate the removal location.
Benefits and how it works
- Reducing the error rate: Employees remove the required parts and confirm the removal, which significantly reduces the error rate.
- Reduce stress and increase efficiency: Visual support speeds up the workflow and reduces stress for employees.
- Automation potential: The system is basically designed in such a way that it can be operated fully automatically, for example with robots or self-propelled cars.
Ergonomic adjustments and warehouse management
- Frequency of use is determined by the arrangement: Parts that are frequently needed are at the bottom and at ergonomically accessible heights, while rarer parts are stored higher.
- Kanban principle for refilling: The back of the flow racks is used for filling according to the FIFO principle (First In, First Out). A sensor system signals the need for refilling, which optimizes material flow and minimizes downtime. Another key advantage of the pick-by-light system combined with the Kanban principle is the proactive refilling of components before they run out. This reliably prevents the production line from coming to a standstill due to lack of materials.
synopsis
The “Pick by Light” system revolutionizes order picking through its intuitive operation and the significant reduction of errors. Coupled with ergonomic improvements and efficient warehouse management, it represents a comprehensive solution to the challenges of order picking.
Project video
A direct look
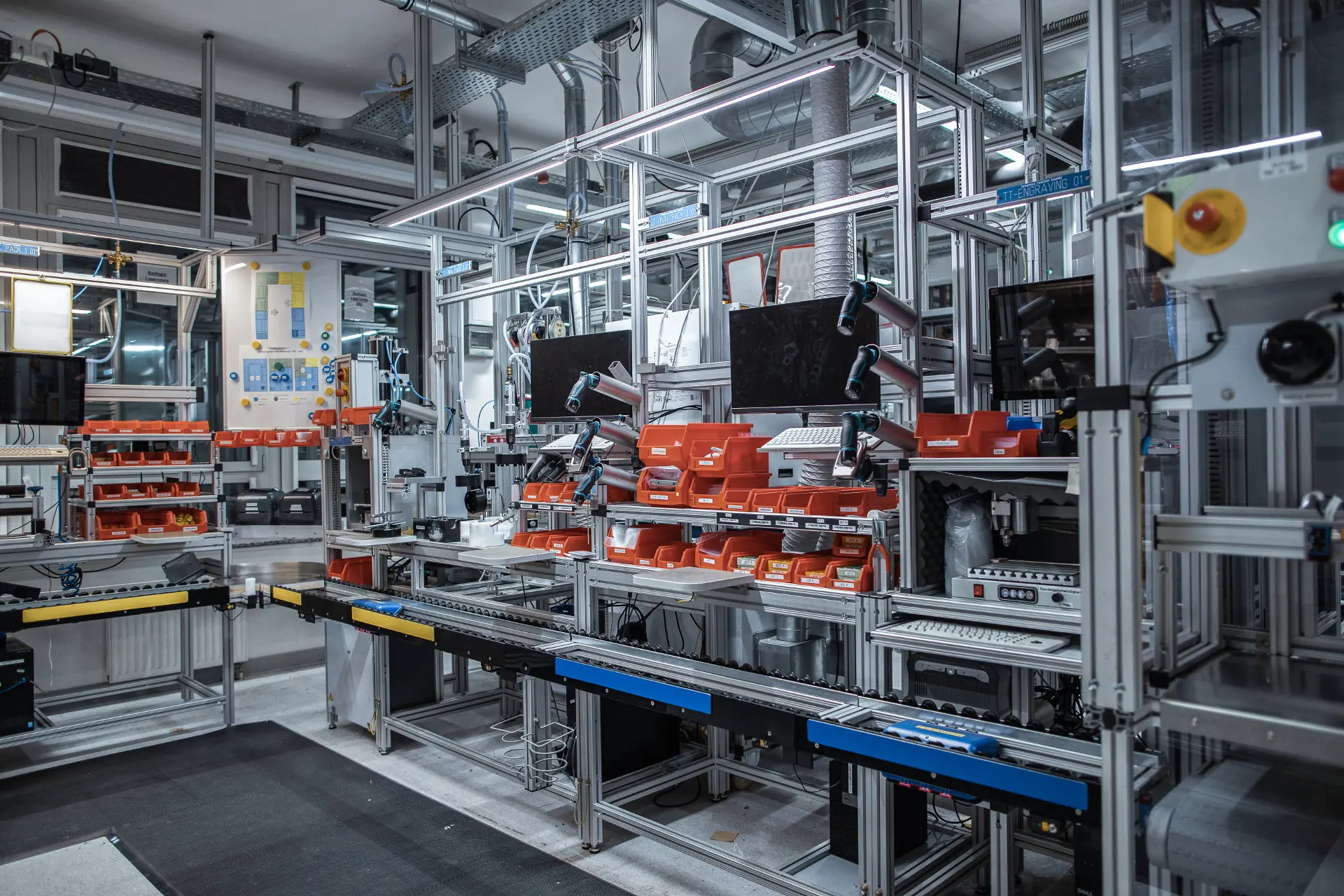
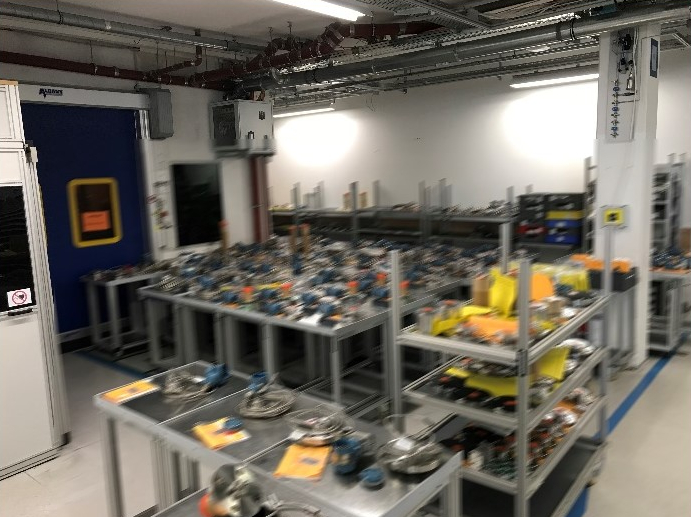